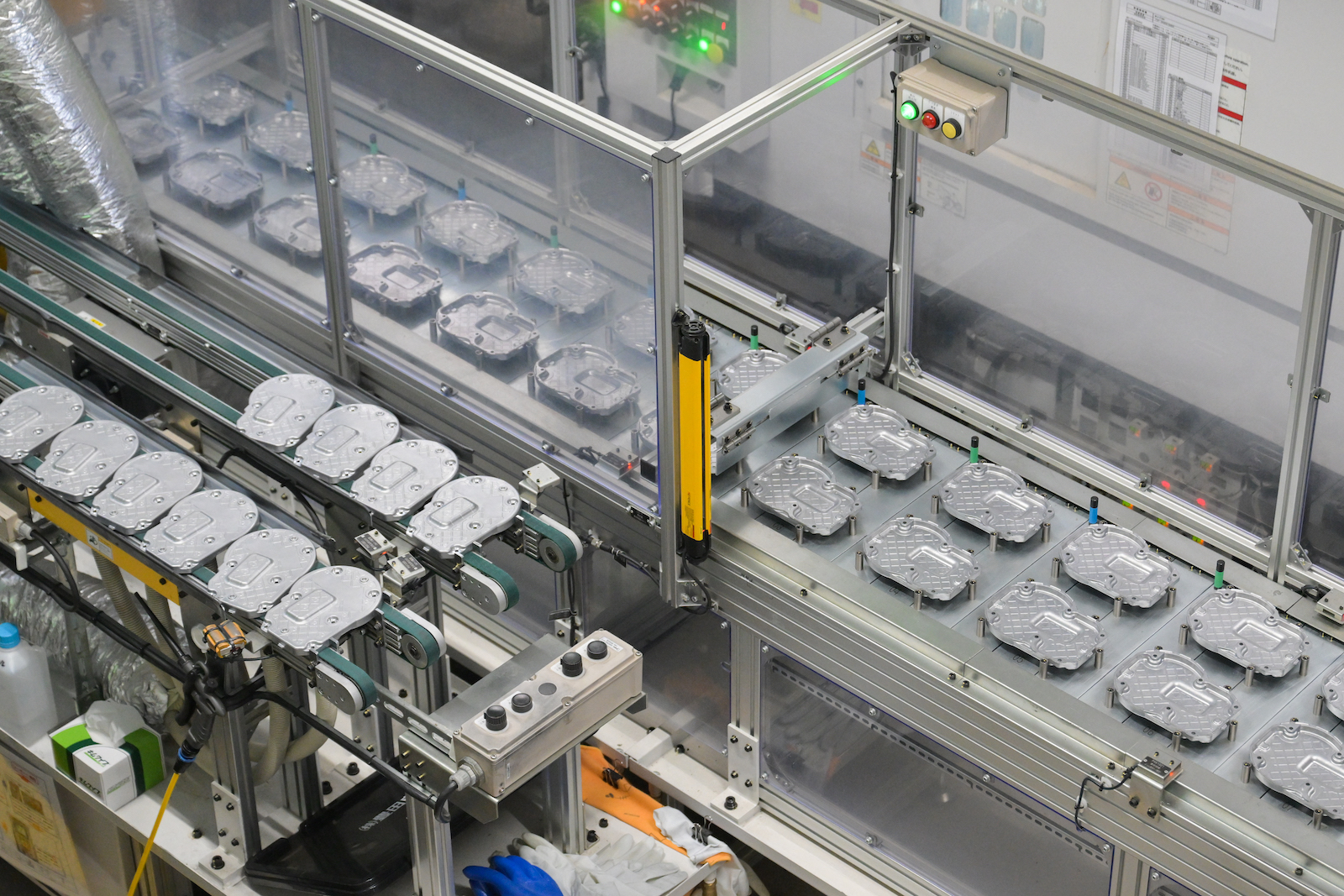
技術×設備の両輪で
挑む、EV新時代
自動車部品、光学部品、産業部品の3分野にまたがるアルミダイカストの一貫生産を手がける株式会社メック。なかでも自動車部品製造は、町工場の経営者たちの間でも「手を出すのは覚悟が必要」と言われる分野だ。納品ロットの大きさ、求められる精度の厳密さ、1年に2度訪れる「価格協力」と呼ばれるコストダウンの交渉。日々高いハードルを超えながら、先を見据えて走り続けることを求められるこの分野で、同社は高い提案力、改善力を強みに顧客の信頼を獲得してきた。そして2021年、3億円規模の大胆な投資で複数ラインの自動化を実現。22年からは本格的にEV(電気自動車)部品の製造にも乗り出した。自動車新時代の一翼となる準備は万全だ。
現場と営業で40年。満を持して社長就任
どこまでも続くかのような、広大な工場の奥深く。出荷前の部品がずらりと居並ぶ部屋に、細かな配線が張り巡らされた機械が置かれていた。
「これが先日設置した、独自の検査機です。社長が開発したものなんです」
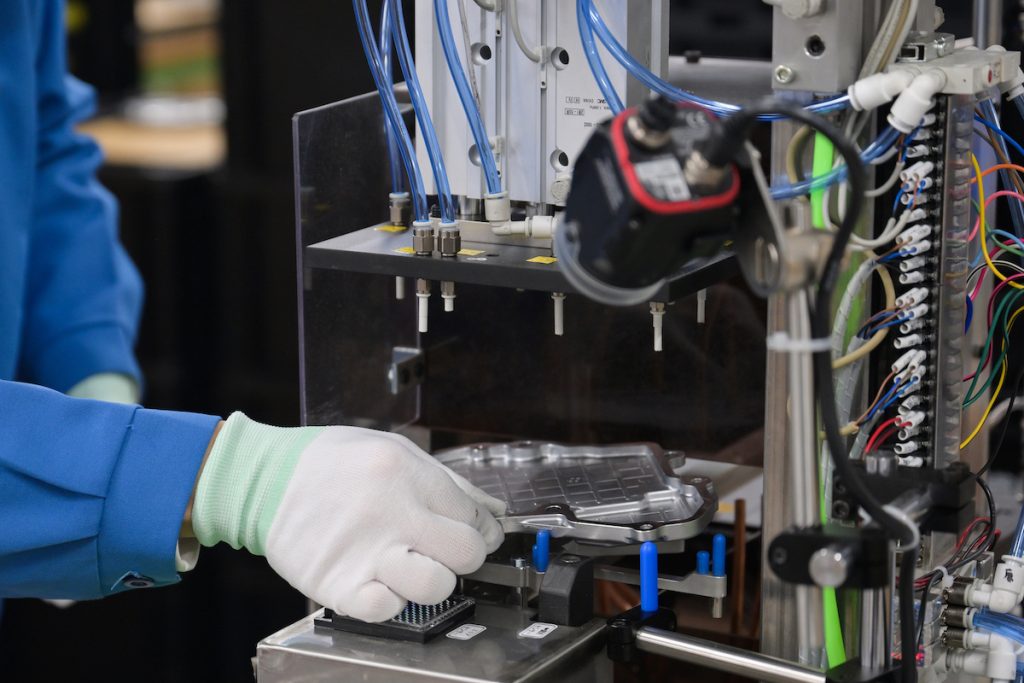
ベテラン社員の一人がそう言って、製品検査の様子を見せてくれた。全体の形状や穴の有無など、部品の特徴的な要素を一つずつ当てはめることで確認し、合致しないものにはアラートが出る──。構造はいたってシンプルだが、この装置の導入により、膨大な検査数でも類似部品の混入を防ぎ、不具合品をより正確にはじくことが可能となったそうだ。
それにしても、100名以上の社員を抱える企業の社長が自ら検査機を作成するとは……。なかなか聞かない話のように思われるが、これこそがメックの真骨頂だ。2022年、満を持して代表取締役に就任したのは、創業家の長男である名取正象。父が小さな亜鉛ダイカスト工場を立ち上げた1982年当初から今まで、ときに製造、ときに営業と多様な役割を一手に担ってきた。
「父が独立後、最初に受注した仕事は、亜鉛ダイカストでつくる腕時計の型枠製造でした。私はその会社に『研修』という名目で人質のようにとられてね(笑)。毎日夕方5時から、自分の会社が納品した製品の不良品を選別する仕事にあたっていたんです。
取引先と自社、つまり家族との板挟みとはこのこと。不良が多ければ伝えなければいけないし、キツかったですよ。でも、この最初の経験があったからこそ、受け取った部品に不良品が入っていたときの取引先の気持ちもよくわかったし、作る側としてはできるかぎりミスを出さないように日々改善していくことの重要性も叩き込まれました」
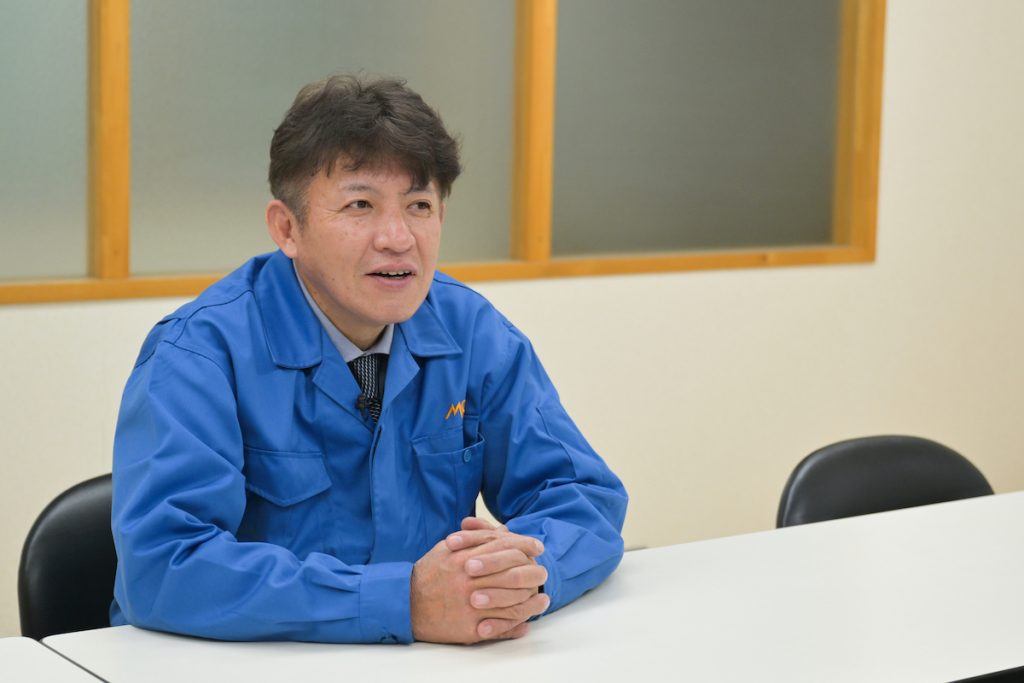
「子どものころから、家にある機械という機械はすべてバラして、暇さえあればいじっていた」という名取はその後、取引先の信頼を獲得するため品質向上の対策を徹底。毎週1回の社内ミーティングで製造工程を見直し改善を続けるとともに、独自の発想で検査体制を整備してきた。その一つが、こうした自作の検査機械や装置の開発というわけだ。
「検査するための“人”を育てることはもちろん大切ですが、人の目で見る検査には必ずミスが生じます。責任はもちろん会社がとりますが、そのとき『失敗してしまった』という気持ちを一生懸命働いている社員に背負わせるのは酷なことだと思うんです。だからこそ、サイズや形状などに合わせて、イエスかノーかはっきりと出る機械や装置を作って、あてはめて確認をしていく。そういう、安心してものづくりができる体制をつくりながら仕事にあたることが、離職率の低下も含めて結局は品質向上の近道になる。おかげで徐々に仕事の幅が広がっていきました」
失敗を経験として生かすチームであるために
1985年にはアルミダイカストの部品受注を開始、1990年には金型・治工具設備の増強を果たし、設計から完成までの一貫生産体制を確立。産業機器部品から工学情報機器部品、そして自動車部品にまで受注の幅を広げていったのもまた、名取の不断の努力の結晶と言える。
製造の現場にも立ちながら週2回、愛知県の取引先まで通い詰める日々は現在も続いている。こうして守り抜いてきた信頼が、現在では大手メーカーの取引設計開発部門から相談を受けるような関係へとつながっているのだ。
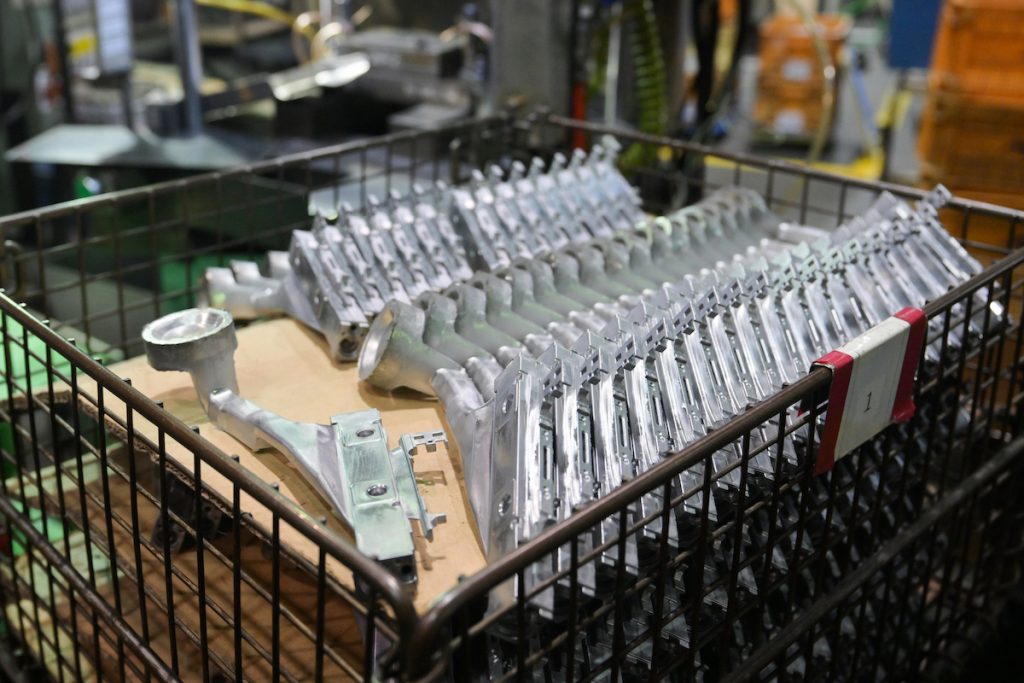
「私自身が今も現場に立つ理由は、自分自身ものづくりが好きだということももちろんあります。でもそれ以上に、本当に今の製造工程がベストなのか、もっと効率よく、品質を上げられる方法はないのかを一緒に現場に立って探り続けたいから。社員はどうしても、『これをやる』と決まったら多少やりづらくてもそういうものだと我慢してやってしまうものです。でも、本当は機械の向きが少し違っていたら動きやすいとか、ここに1つ検査の工程を入れたらムダがグッと減るとか、そういう可能性が潜んでいることは多い。そこに日々、切り込み続けることが当社の強みになっていくと考えています」
この改善はもちろん社長一人だけで行っているものではない。社内に編成されたチームが、社長の指揮のもと必要に応じた検査器具の開発やラインの調整などを担っている。
「製造ラインは、一度で完璧なものが作れるとは限りません。それなのに今、失敗が許される場面が少なすぎると思うんです。失敗は経験。うちはお客様に見えないところなら、たくさん失敗をしていい。その失敗を学びとし、技術者を育てていくプロジェクトチームでありたいと思っています」
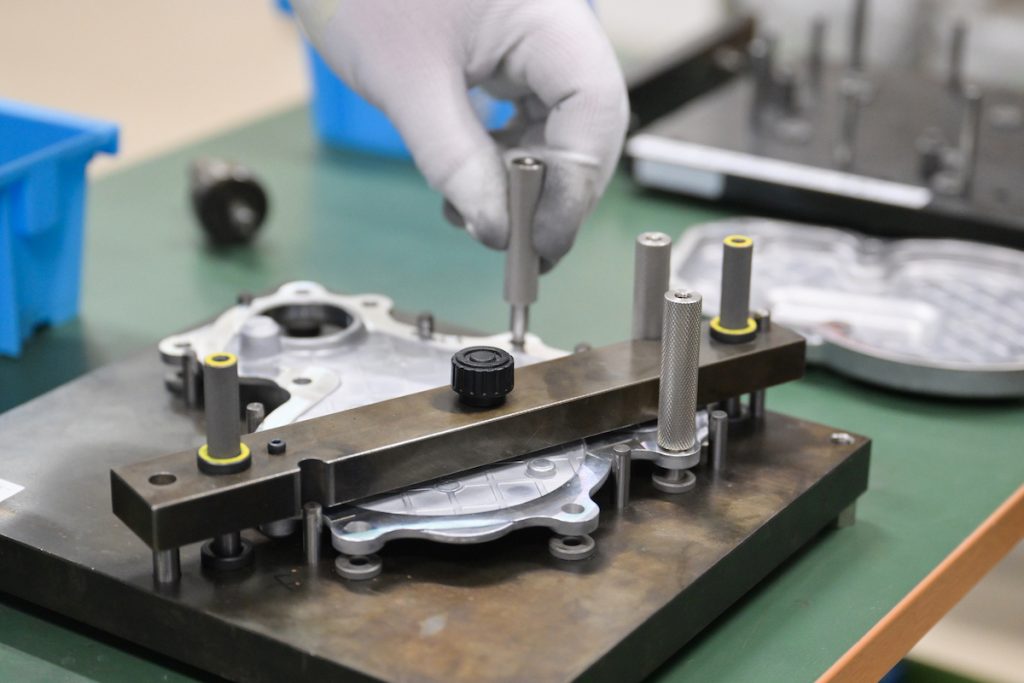
また一方で、現場での知見をもとに、コストを抑えながら部品を一貫生産するため、部品そのものの設計から提案できるのが強みだと名取は言う。
「求められる機能を備えたうえで、作りやすく、コストを抑えた部品を提案する。それは結果的に取引先のためにもなるからこそ、喜んでいただき次の受注につながるのだと思います」
大規模自動化+応力カットの新システムで、EV新時代に万全の体制
日々の改善力と、受注時の提案力。ここにさらなる強みを加えるべく、メックは次なる展開に動き出した。まずは2021年、3億円規模の融資を受け、ダイカストマシン350トンを増設し、プレスの自動化を実現。これにより、高精度な自動車部品の生産量が飛躍的に向上した。
そして今取り組んでいるのが、アルミの鋳造時に生じるひずみの調整を自動ラインのなかで行う、という画期的な応力カットシステムの構築だ。ガソリン車と比べてEV車は、部品点数が1/3にまで減少すると言われている。EVシフトが進む今、メックがこの先も自動車部品製造で選ばれ続けるための準備は万全に整いつつある。
「かなりお金をかけたので、受注がなかったらどうしよう、と思っていましたよ」と笑うが、結果は予想以上。世界一の電気自動車メーカーの部品受注も獲得し、名取の社長就任元年であった2022年は創業40年にして最高の売り上げを叩き出した。
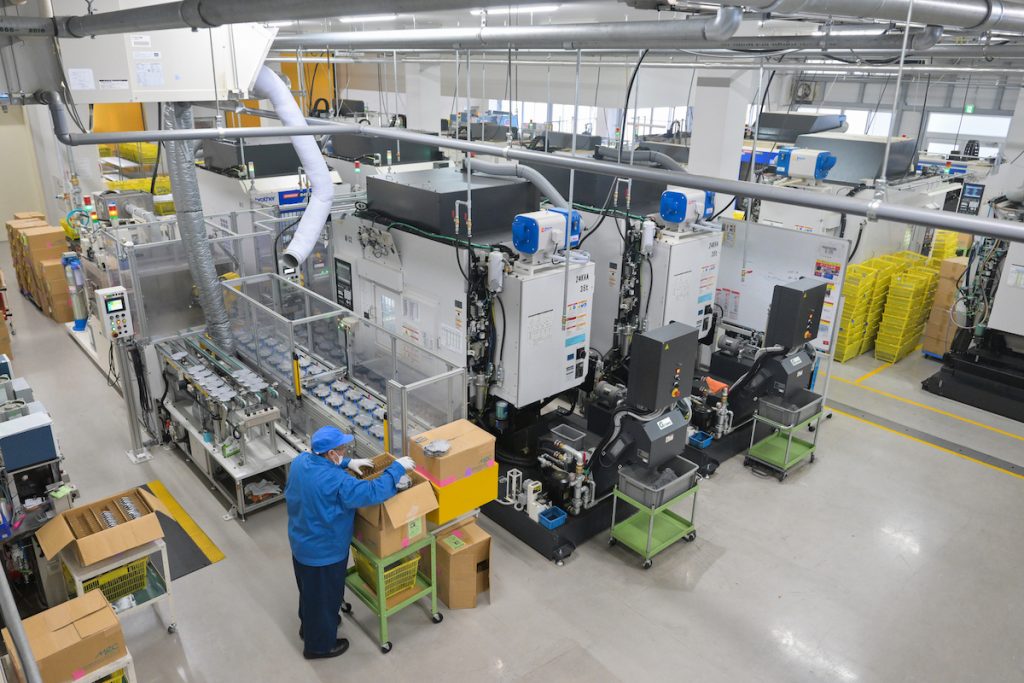
「多くの部品を担わせていただき、開発にも関わらせていただけるようになってきたここ数年は、『これからどうする、もうワンランク上がってこいよ』というメッセージを受け取っている期間だと思っていました。この、自動化の準備が整ったことで、やっと社長に就任できました」と名取。そして最後に真剣なまなざしで、こう付け加えた。
「はじめて自動車部品を受注したとき、お取引先様に言われた言葉は、今も忘れません。『もし100万個に1個だったとしても、不具合があれば事故につながる、最悪の場合命が失われてしまう。お願いしているのは、そういう部品なんです』と。コストは下げ、精度は高めて量産を実現しながら、命を守るための部品を間違いなく納めていく。私たちはそういう挑戦をさせてもらっているんです」
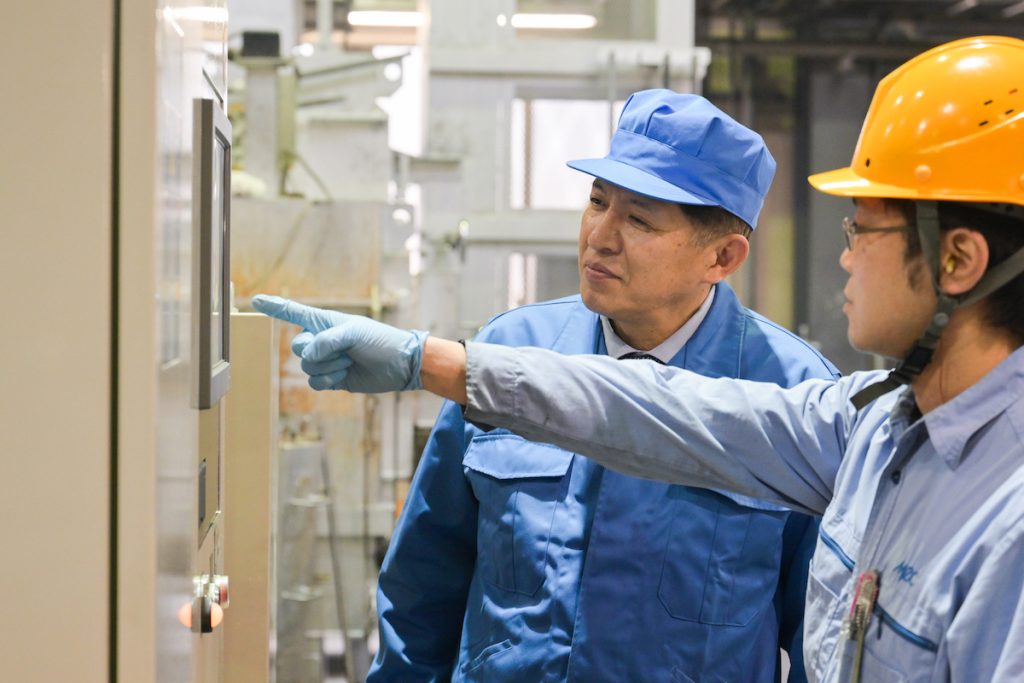
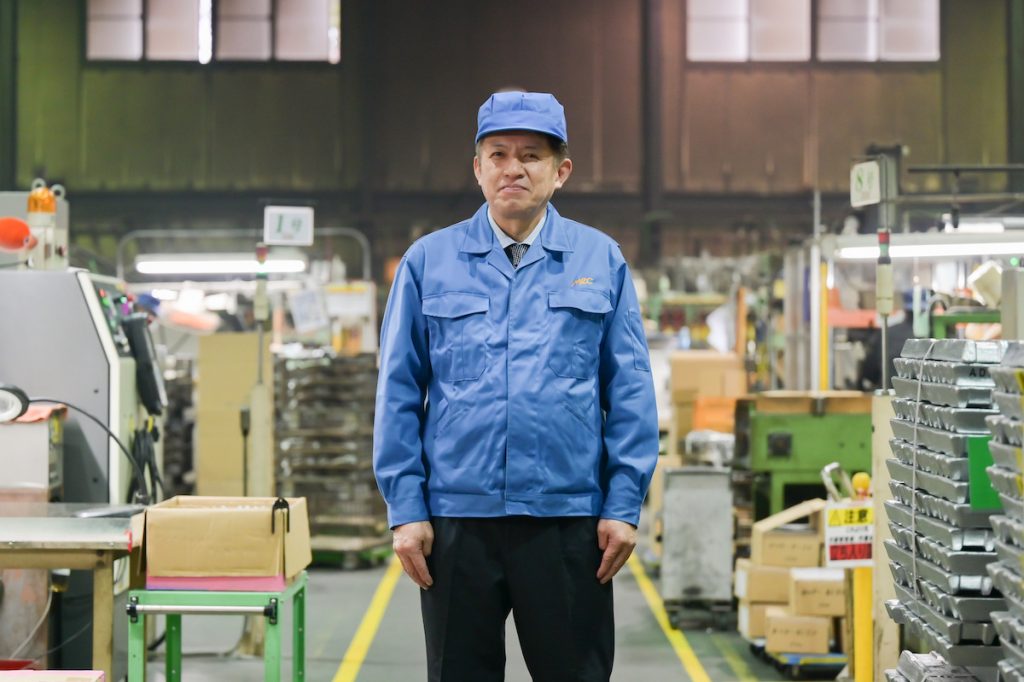
取材・執筆:玉木美企子
構成・編集:栗原大介(ヤツメディア)
写真:五味貴志
動画:山田智大(やまかめ)
株式会社メック
【設立】1982年
【住所】〒399-0211 長野県諏訪郡富士見町富士見248-34
【連絡先】TEL:0266-62-4855 FAX:0266-62-5571
【代表者】 代表取締役 名取正象
【従業員数】103名
【事業内容】自動車部品、情報機器、産業用機器のアルミニウムダイカスト製品製造、金型設計・製作
【主要取引先】アルバック機工株式会社、株式会社ATA、エヌティーテクノ株式会社、 京セラ株式会社、佐藤金属株式会社、住友電装株式会社、大豊工業株式会社、株式会社タムロン、中央発條株式会社、株式会社豊田自動織機(敬称略・五十音順)
【主力製品】自動車部品、情報機器、産業用機器のアルミダイカスト製品の製造、金型および治工具の設計・製作
【設備情報】ダイカストマシン(50t)1基・(90t)2基・(125t)1 基・(135t)6 基・(350t)3基 、DC試削り用旋盤2基、立型フライス盤1基、CNC旋盤3基他/マシニングセンター16基、タッピングマシン4基、タッピングセンター4基、CNC タッピングセンター5 基他/研掃機関連アニール炉2基、回転バレル1基、研掃機5基、振動バレル3基、ショットブラスター2基
〔測定機〕三次元測定機4基、CNC三次元測定機1基、真円度測定機1基、面粗度計1基、画像測定機1基 ほか
【webサイト】http://www.kkmec.co.jp/
(記載の内容は全て取材時点の情報です)

株式会社メックへの
お問い合わせはこちら
SEIMITSU FUJIMI の情報をメールでお届けします!