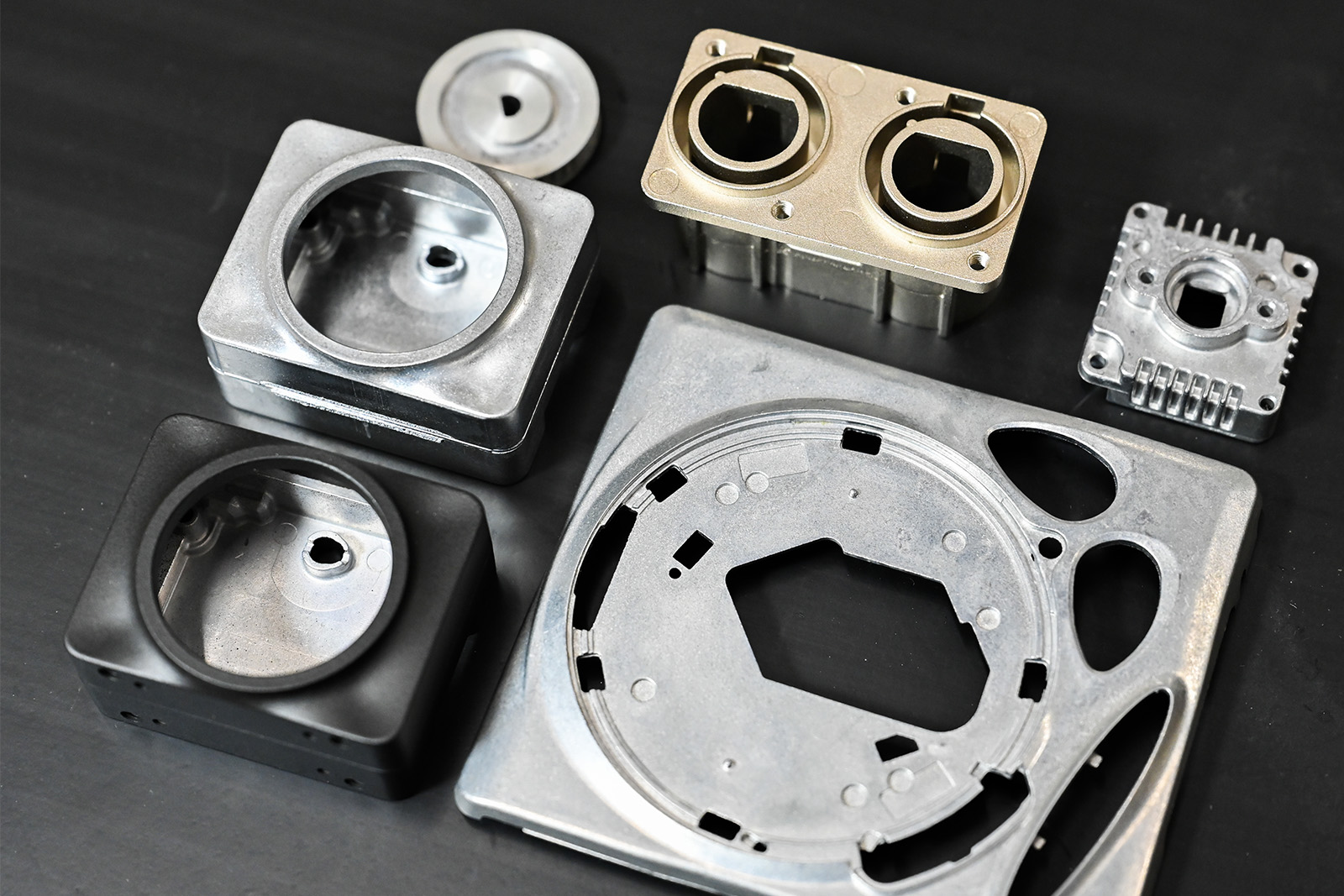
ダイカストで
0.5mmの極薄化を実現
富士見町のものづくり産業を発展させた背景のひとつに、光学部品製造がある。日本がカメラブームに沸いた1960年代、富士見町、そして諏訪一帯では多くの企業がこれに取り組み、供給を支えてきた。しかし、事業の継続に大切なのはブームの「その後」。みやま工業は、積み上げた経験をさらに先鋭化させることで、小型・薄型化時代のものづくり集団として圧倒的な存在感を放っている。
アルミダイカストで小型・薄型を先鋭化。
「0.8mmなら余裕を持ってお受けできます」
「この前、うれしいことがあって。NASAに関連する企業から、『あなたたちが手掛けたカメラハウジングとレンズホルダーが火星に到達しました。火星着陸時に そのカメラが記録した映像が調査に役立っています』ってメールが届いたんです」
出会い頭に、代表取締役社長・小林昭彦から予想外の話題が飛び出した。富士見から、火星(NASA)へ!?思わず聞き返すと、こんな答えがかえってきた。
「そうなんです。弊社は創業当時からミラーボックスをはじめ、カメラ本体に入っている部品の製造を手掛けてきました。この技術を特化させて、薄物、小物分野で先鋭化してきた。その成果のひとつがこうして現れて、しかもわざわざご連絡までいただいて。私たちもやりがいを改めて感じているところです」
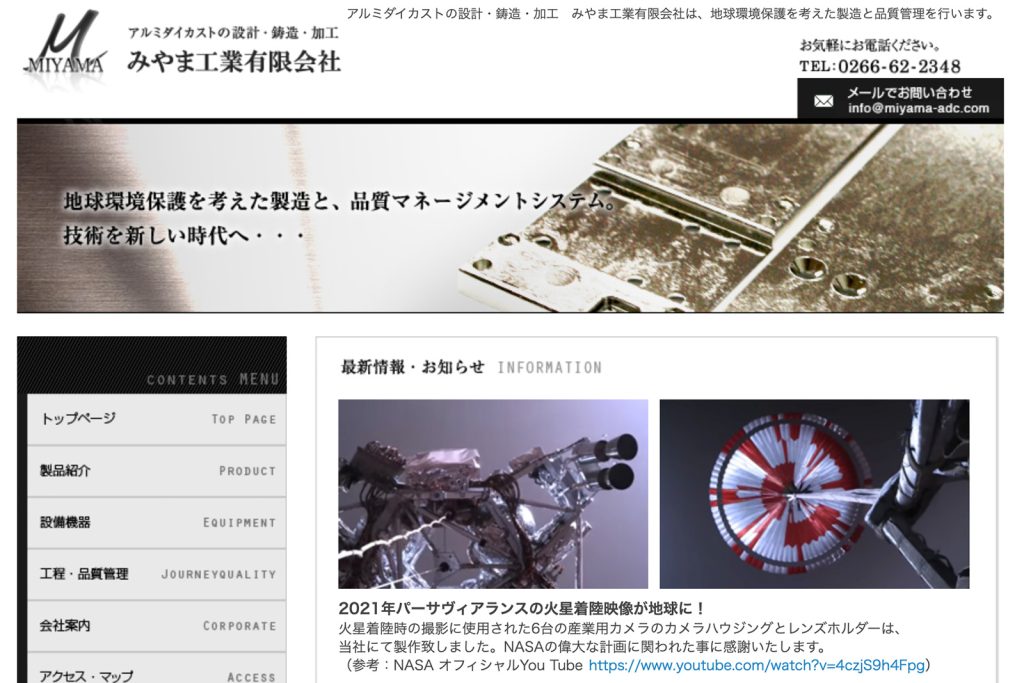
NASA撮影の公開動画/みやま工業ウェブサイトから
光学部品製造といえば、ひところの富士見町・諏訪地域では「石を投げれば当たる」と言われるほど多くの工場が手掛けていた事業だった。しかし、カメラブームの終焉とともに受注は激減、大半の企業がより収益が見込める事業へ転換した。廃業に追い込まれた企業も多く、今も「光学は事業としての主力にはなり得ない」、との見方が一般的ではないだろうか。
しかし、みやま工業ではその後もこの技術の先鋭化に邁進し続け、アルミニウムダイカスト(以下、アルミダイカスト)での小物・薄物技術で徐々に業界の存在感を示すように。その評価の一つの表れが、このNASA関連企業からの受注だったと言えるだろう。
一眼レフカメラのミラーボックスやフレームを原点に、カーオーディオ、家電、ヒートシンク(放熱版)小型マシンビジョンカメラなど、徐々に受注分野の幅を広げてきた同社。とくに「他の追随を許さない」と言われているのが、仕上がりの「薄さ」だ。
「形状によって技術的には0.5mmまで可能ですが、製品として量産するなら0.6mm以上をおすすめしています。0.8mmと言われれば、『それなら余裕だな』というのが、今の感覚ですね」息子であり工場長・小林浩樹のそんな言葉に、社長の昭彦も笑顔で頷く。これこそが名だたる企業をして「みやま工業にしか頼めない」と言わしめる技術力なのだ。
極薄化に欠かせない低温・低圧鋳造と、
それを可能にした金型の設計力
アルミダイカストでの量産品製造で0.6mmの極薄化を実現。そのような離れ業を、どのように確立してきたのだろう。その理由の一つは、この仕事を知る者なら金型をひと目見ればわかるかもしれない。
「ちょっと、常識では考えられないような形をしていると思います」
社長・昭彦の言葉が意味するのは、金型がつくりだす部品の“周辺”、いわゆるゲートやランナー、そしてガス抜きのオーバーフロー部分の特徴だ。
「最初は金型屋さんに『こんな型でモノになるのか』と笑われた」というその形状は、現在の一般的なアルミダイカストよりもはるかに低い温度と圧力で仕上げる「低温・低圧鋳造」のために生み出されたもの。この「低温・低圧」と、それを実現する金型づくりによって、同社では他の追随を許さない極薄部品の量産化を実現しているのだ。
「ダイカストにおける一般的なアルミの融解温度は690~700℃ですが、私たちは640~650℃で行っているんです。いま、アルミダイカスト業界が他社が行っている部品製造の多くは”厚物”と言われる自動車の部品がほとんど。この技術は安価に部品を量産することに長けているものですが、繊細な薄物・小物を安定して量産させるのは難しいと、ほとんどのダイカスト屋が嫌がるんです。
けれど、私たちは大量受注(自動車の部品)がストップしたときの苦い経験から、生き残り策としてあえて大物には手を出さず、薄物・小物に特化しようと考えた。そのなかで生まれたのが、この低温・低圧鋳造の技術なんです」
そして、この極薄部品製造で重要なのはとくに「低温」であることなのだと社長・昭彦は話す。
しかし、融解温度が高くなればなるほど粘度が低くなり、あらゆる型になじむ「扱いやすさ」が生まれるように感じるが、なぜ低温でなければいけなかったのだろう。そんな疑問に、息子であり工場長の浩樹はこう説明した。
「単純な話、熱いものに圧をかけたら、そのぶん金型に加わる抵抗が大きいですよね。加えてもちろん熱いものは冷やさなければならない。そうすると、その温度の高さや、高い圧力の分だけ、金型にも傷みが生じてしまい、精度の高い薄物を安定的に量産することが出来ません。大物ならばそれでいいのですが、小物・薄物を極めようと思ったら、この低温・低圧技術が欠かせないと私たちは考えています」
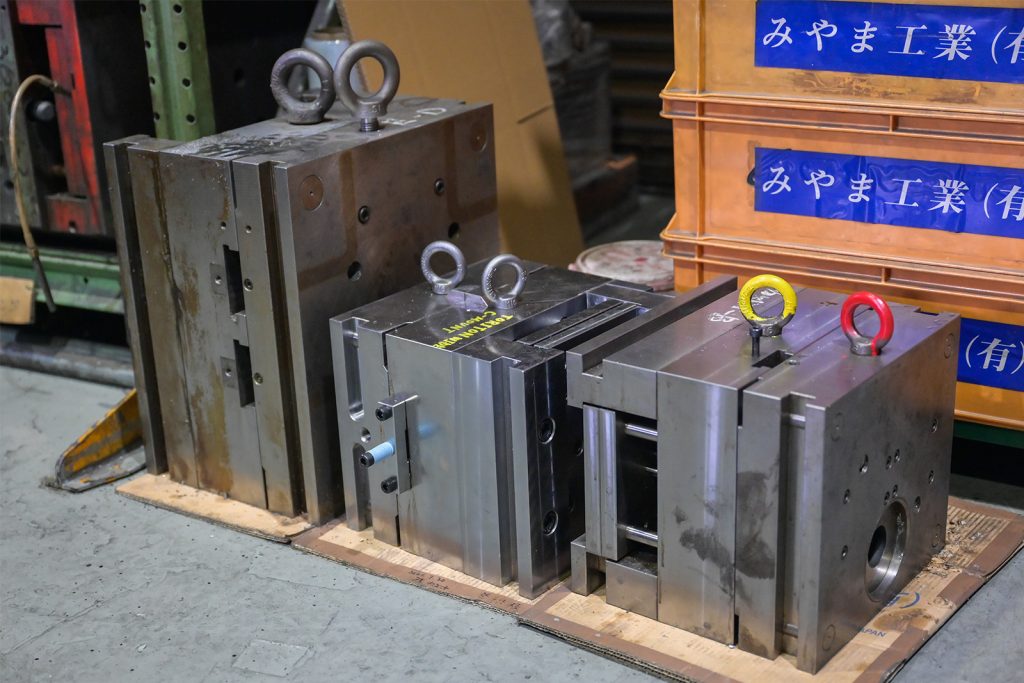
極薄化のための工夫は、「約30年前に盛んになったマグネシウムダイカストに負けない技術をと取り組んだのが大きなきっかけでした」と社長は話す
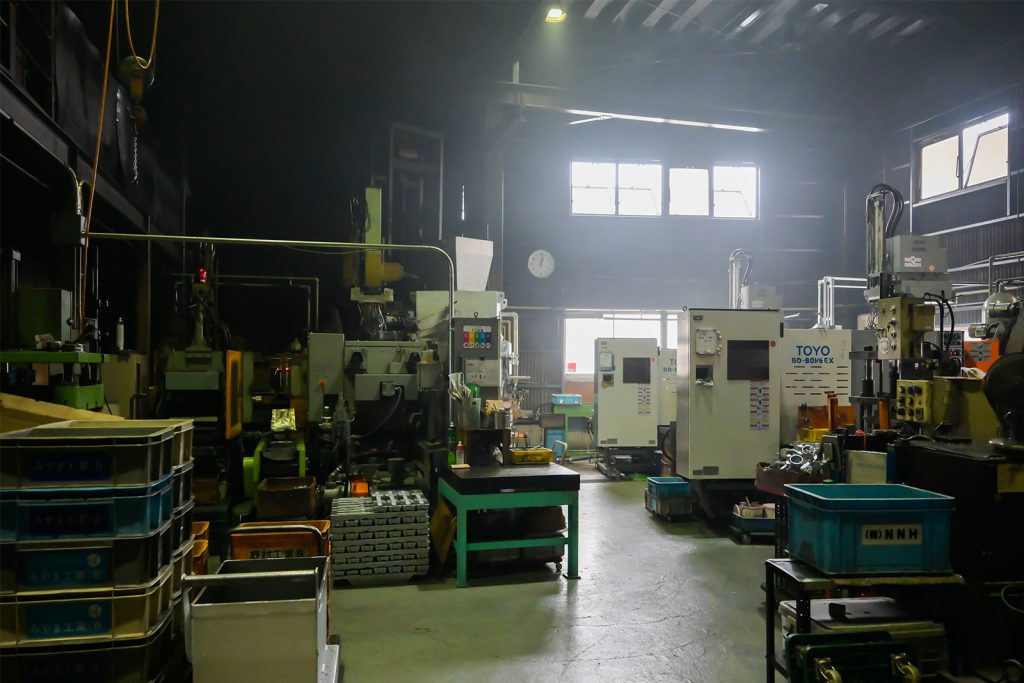
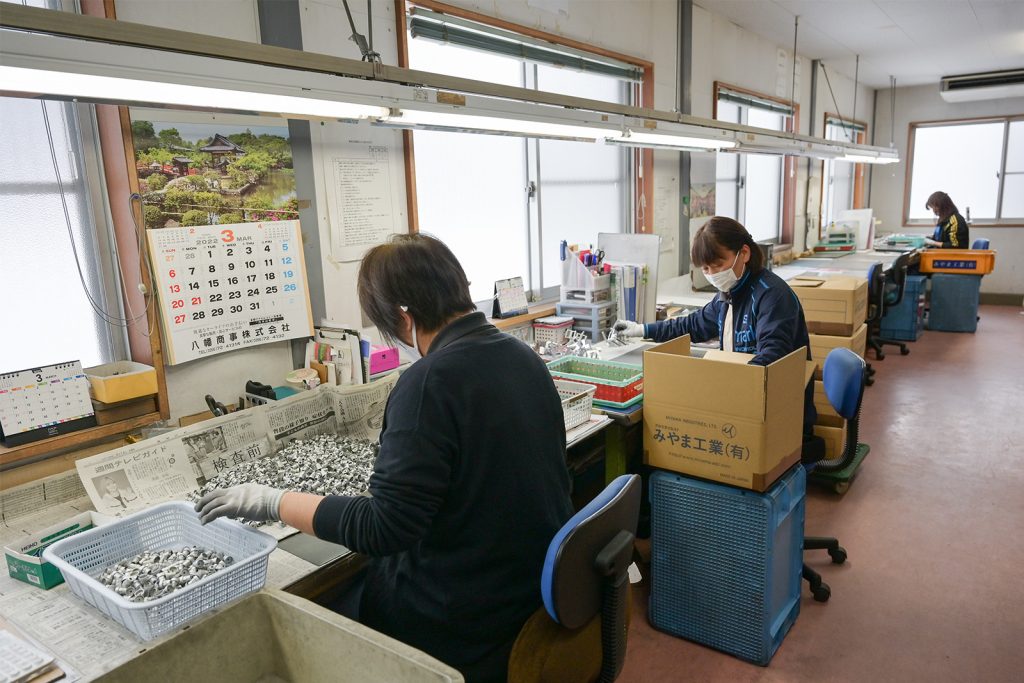
低温・低圧鋳造がもたらす「型の長寿命化」で大幅なコスト削減を実現
低温・低圧を武器に信頼を獲得してきたみやま工業。その「強さ」を象徴するような、こんなエピソードもある。
「あるとき、うちともう一社の二社で同じ製品の生産に取り組んだときのことですが、もう一社は、製品の生産回数がうちの半分ぐらいの時点で型が傷んでしまったんです。そのときの部品は『低温・低圧でなければ』というほどの薄さではありませんでしたが、結局、こちらで用意していた予備を提供したこともありました。
あまりにもうちの型が長持ちすることに驚かれたそのとき、低温鋳造の利点と、父が培ってきた金型設計のすごさを改めて実感しました」(浩樹工場長)
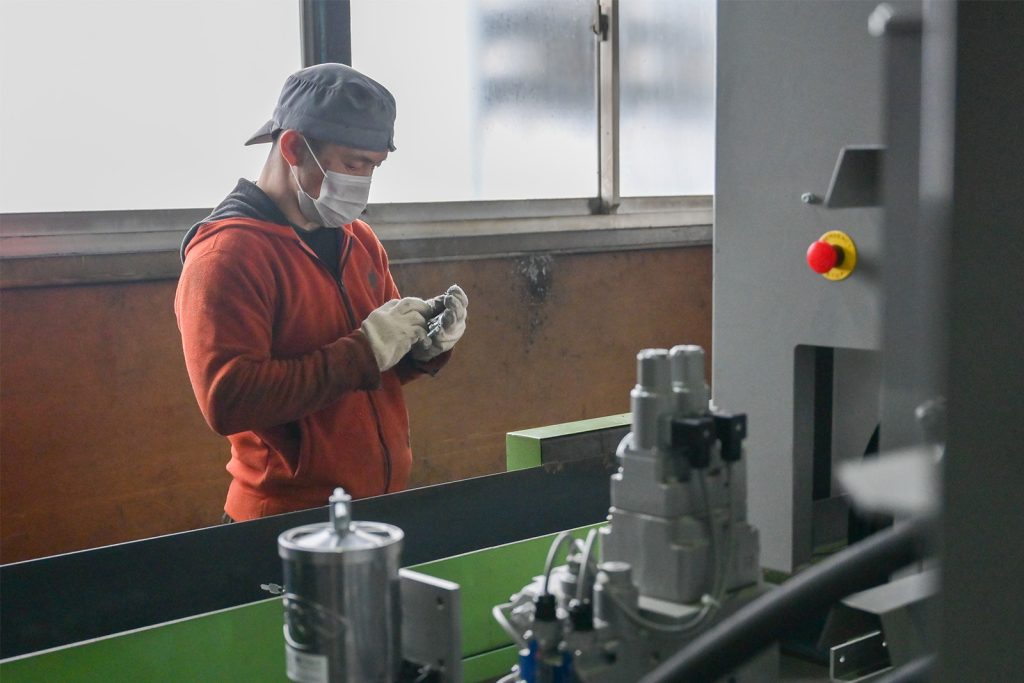
部品生産においてもっともコストを要する金型。一つの金型で何個までを製造するのかをあらかじめ設定するいわゆる「保障ショット」は、ともすれば仕上がり品の価格にさえ影響するほど、コスト管理において需要なポイントだ。この保障ショットが、みやま工業の低温・低温低圧鋳造なら、一般的なアルミダイカストのほぼ倍量で設定可能なのだとか。
「僕はもともと、職人気質ではないんです。だから若いころ、職人たちの仕事をひたすら目で見て覚えた。すべて独学だから、常識がなくてね(笑)。自由な発想があったのかもしれません」(昭彦社長)
じつはこの低温「640℃」の背景にも、現場で見て学んだ経験がある。今でこそ、溶かしたアルミを型に流し込むのはロボットの仕事だが、昭彦社長が会社に入った当時はまだ、職人が柄杓ですくって流し込んでいた時代。そのころのアルミの温度がまさに、いま同社が扱っているのと同じ640℃だったのだという。
「ダイカストにおけるアルミの温度が上がった理由は、『ロボット』なんですよ。ロボットが導入されはじめた当時、まだロボットアームが滑らかに動かなかったから、その温度では粘度が高すぎて、仕事にならなかった。そこで、業界全体が温度を上げて対応した、という歴史があるんです。
その手作業の経験を覚えていたから、現在のロボットアームなら『温度を下げてもいけるよな』という感覚があった。独自の発想ではなく、ちょっとした技術の応用なんです」
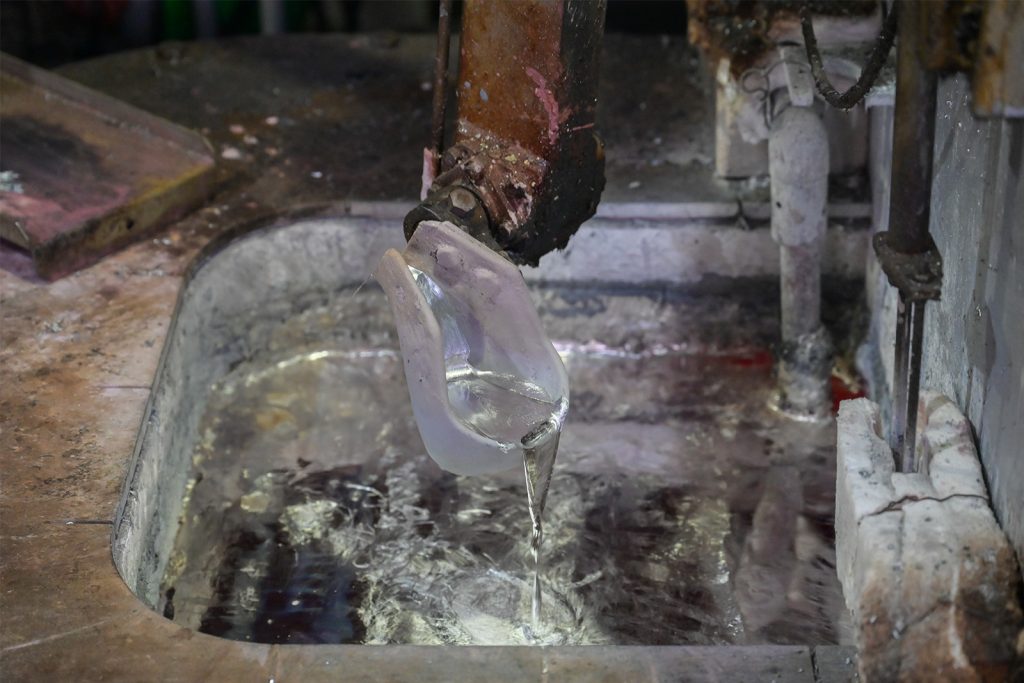
「会社の顔は社員」。チームが輝く企業をめざして
こうして、今や幅広い分野のものづくりの一翼を担うみやま工業。さらなる体制整備としてワンストップの納品をめざし、2015年にはマシニングセンターも導入。2019年には二次加工専門の第二工場も建設した。
「手探りでしたが、お客様にご満足いただける二次加工ができるようになってきました。さらに塗装、印刷までを協力会社の連携もあおぎながら実施し、完成品で納める仕事が増えています」と浩樹工場長。検査体制も18人の社員のうち10名以上をあて、品質管理には大きなリソースを割いている。
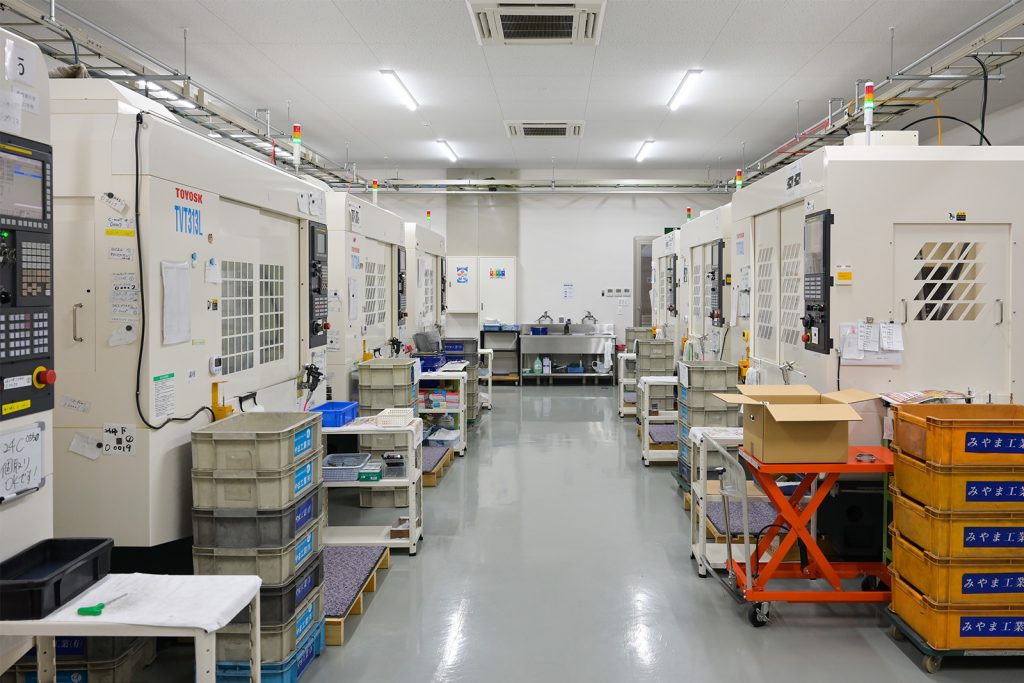
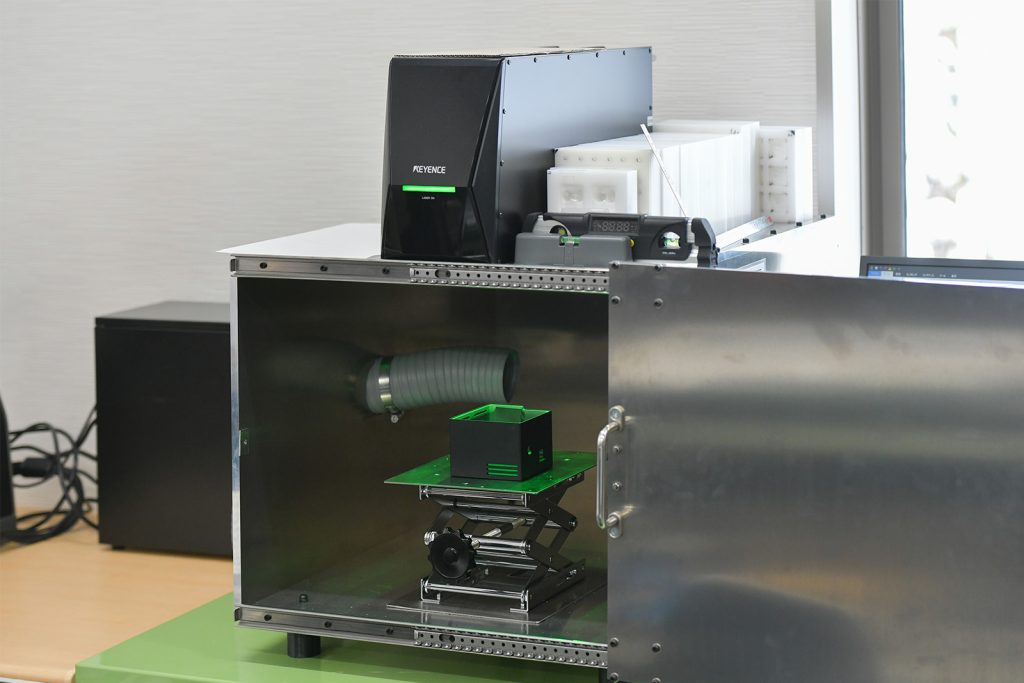
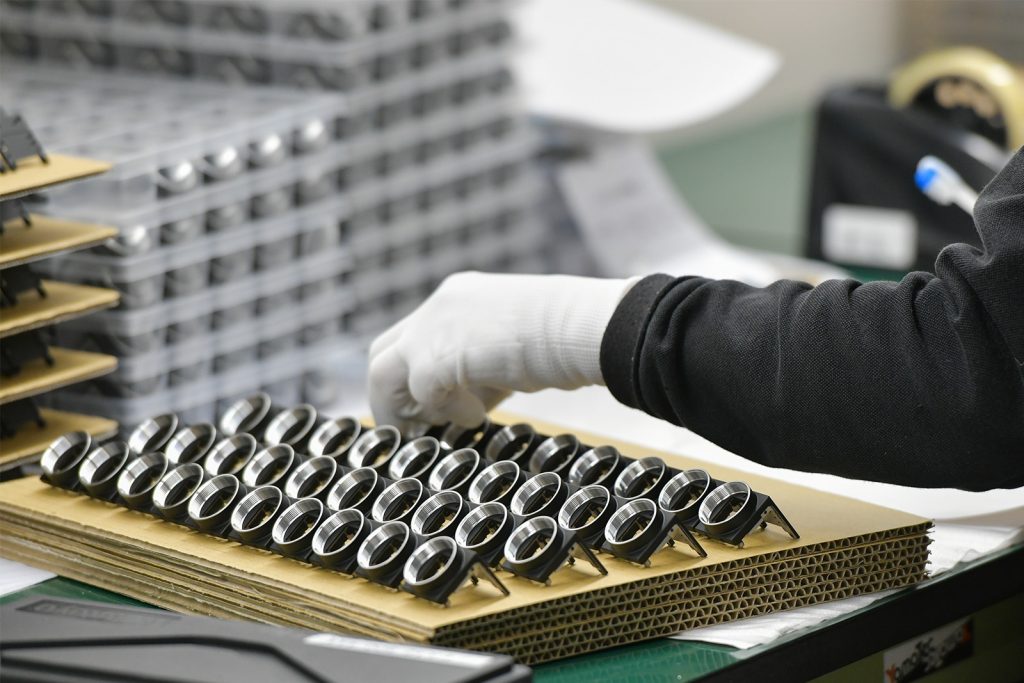
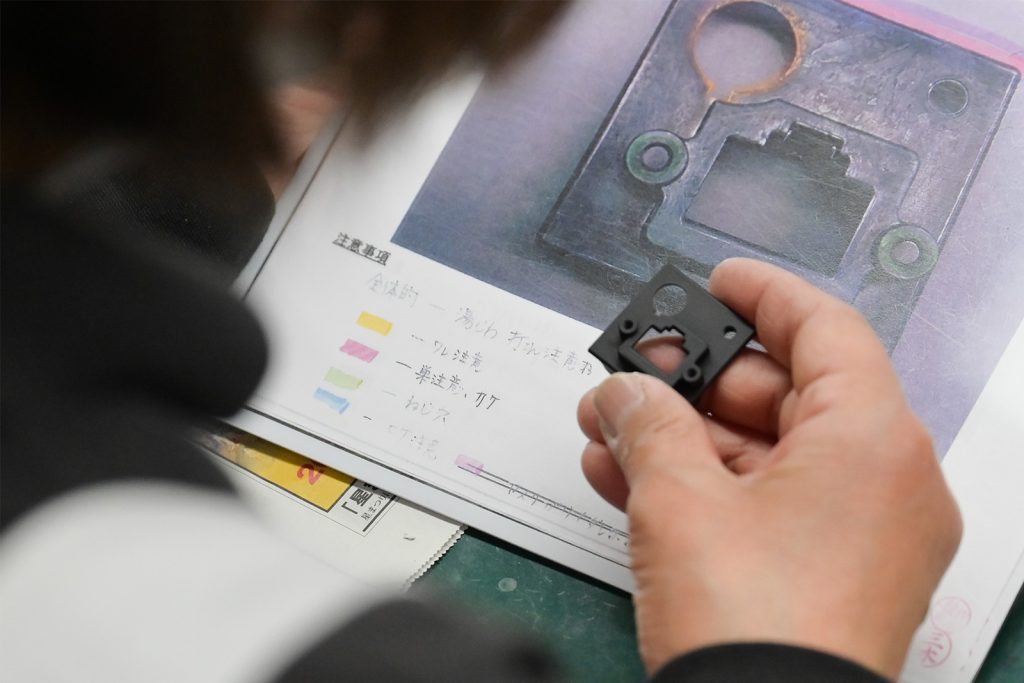
こうした進化に伴い、事業体制も社長の昭彦から息子で工場長の浩樹主導のものへと徐々に移行中。コア技術と言える金型の設計も、そのほとんどを受け継いで実施できるまでになってきた。
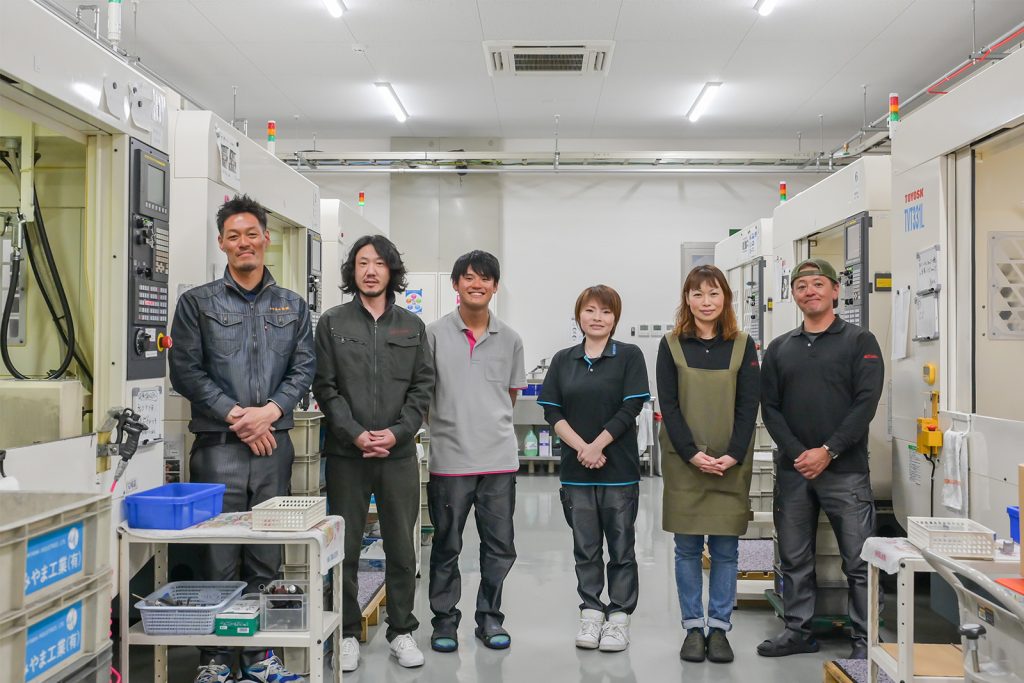
「それでもね、まだまだ現社長のあり方にはかないません。今年に入ってから、『そろそろ俺がやるから少しゆっくりすれば』と社長に促して、3日ほど朝6時半に出社するようになったのですが、すぐにまた朝5時頃、誰よりも早く出社しているんですから(笑)」(工場長・浩樹)
「でも、これからは社長が一人で引っ張っていく時代じゃないから。今後のために私から伝えているのは、仕事うんぬんよりも『従業員から信頼される存在であるように』、ということだけですね。人格が育てば、そのように仕事にも向き合うでしょうから」(昭彦社長)
最後に、浩樹工場長からはこんな依頼があったことを書き添えておこう。
「僕たちの写真はいいですから、ぜひ社員を前に出してください。この会社を支えているのはここで働く一人ひとりの力なんです」
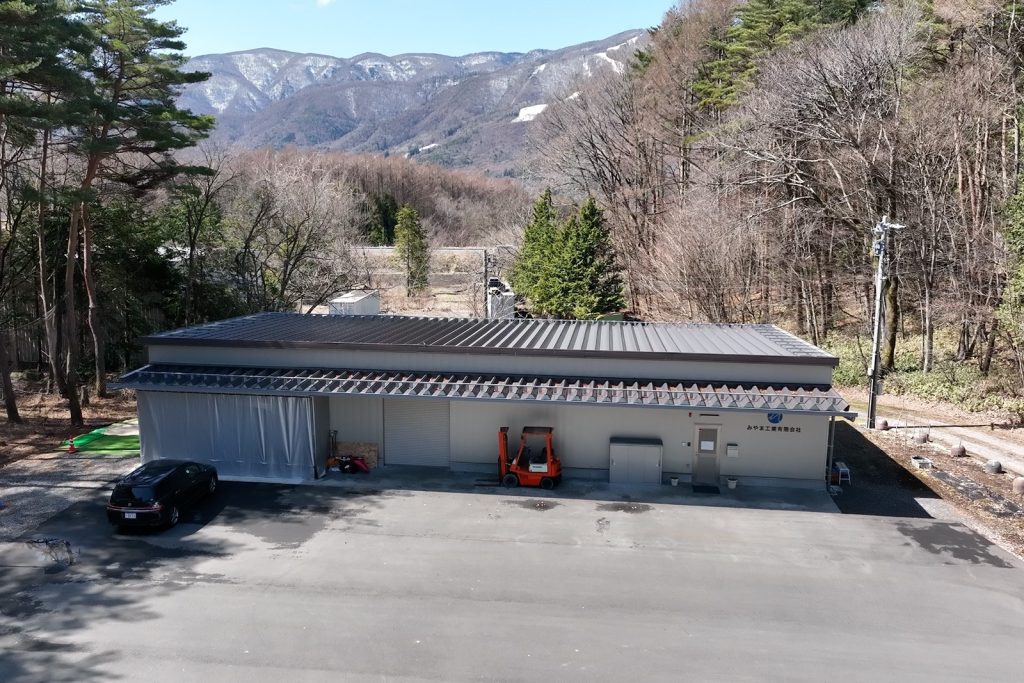
取材・執筆:玉木美企子
構成・編集:澤井理恵(ヤツメディア)
写真:五味貴志
動画:山田智大(やまかめ)
みやま工業有限会社
【設立】1973年
【所在地】長野県諏訪郡富士見町富士見25
【連絡先】TEL 0266-62-2348
【代表者】代表取締役 小林昭彦
【従業員数】16名
【事業内容】アルミダイカストの鋳造・加工・表面処理・金型手配 他、デザイン・ウェブデザイン制作
【保有資格】ISO 9001:2015 認証登録工場
【webサイト】https://www.miyama-adc.com/
(記載の内容は全て取材時点の情報です)

みやま工業有限会社への
お問い合わせはこちら
SEIMITSU FUJIMI の情報をメールでお届けします!